Benefícios obtidos com o Controle Avançado
Os benefícios que podem ser obtidos com o uso de Controle Avançado em uma planta industrial estão sempre relacionados a reduzir a variabilidade de uma variável economicamente importante, chamada de variável crítica, e deslocar seu valor médio (“set-point”) mais próximo aos valores de especificações e limitações impostos pelo processo. Considere um reator no qual o aumento da temperatura de reação leva a um aumento no rendimento do produto. Existe, entretanto, um valor máximo para esta temperatura acima do qual haverá uma degradação na qualidade do produto ultrapassando sua especificação. A operação com baixa temperatura acarretaria perda de rendimento e desperdício de matéria-prima, e a operação acima do limite causaria refugo ou perda do produto fora de especificação. Idealmente deveríamos operar com esta temperatura sempre no valor do limite máximo. A figura 1 mostra um gráfico típico de variação ao longo do tempo para três situações de diferente desempenho no controle desta variável crítica.
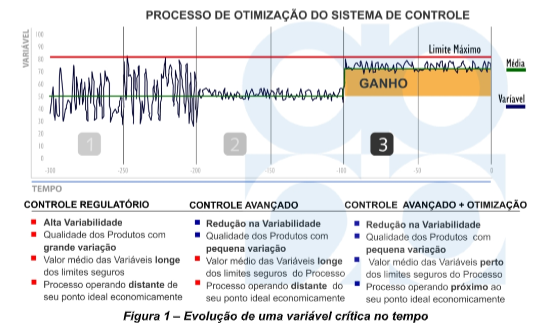
Na prática sempre existe variabilidade e teremos que operar com o valor médio desta temperatura abaixo do limite máximo de forma a não violar a especificação do produto conforme a msituação 1. O uso de Controle Avançado permite reduzir a variabilidade (situação 2) e aproximar o valor médio do limite superior (situação 3). De forma geral, podemos sempre relacionar uma redução de variabilidade e aproximação do valor médio de uma variável crítica aos limites do processo com fatores econômicos da planta que poderão ser tipicamente um ou mais dos seguintes: Aumento na capacidade de produção; aumento no rendimento de produtos; redução de perdas; redução da sobre especificação; redução no consumo de energia; redução no consumo de produtos químicos; redução do custo operacional; melhor qualidade dos produtos; melhor qualidade dos efluentes líquidos e gasosos (podendo gerar crédito de carbono).
Os benefícios com Controle Avançado em plantas industriais devem ser sempre medidos e quantificados para que possamos justificar economicamente os investimentos. A maneira mais simples de fazer isto é quantificar estatisticamente a redução de variabilidade por meio de seu desvio padrão, e o deslocamento do valor médio antes e depois da implementação do CA relacionando este deslocamento com fatores econômicos do processo de produção [2]. A experiência de implementação de projetos de Controle Avançado e Otimização têm demonstrado grandes benefícios econômicos. São relatados benefícios obtidos que variam de 2 a 13 milhões de U$/ano para aplicações na área de petróleo e petroquímica [3,4]. O retorno do investimento é bastante rápido, com tempos geralmente menores que 6 meses. Tivemos oportunidade de participar de projetos de CA na área do refino de petróleo, um dos quais em uma unidade de Craqueamento de Fluido Catalítico (FCC) apresentou benefícios da ordem de US$ 3,5 milhões por ano [5], no final da década de 90, quando o barril de petróleo estava na faixa de US$ 20,00 a US$ 30,00.
Como fazer uma boa aplicação Controle Avançado
Nas plantas de processo os desempenhos individuais de cada malha de controle contribuem sequencialmente para gerar a variabilidade total. As variabilidades são propagadas ao longo dos equipamentos e malhas de controle sofrendo atenuações ou amplificações. Desta forma torna-se imprescindível considerar a planta como um todo em um projeto de CA. As estratégias de controle devem ser analisadas conforme sua importância para estabilizar o processo de forma global. É de fundamental importância o bom entendimento do processo em questão, seus objetivos, seus princípios, suas operações unitárias e suas características de operação.
Podemos visualizar um bom procedimento para um projeto de otimização de controle como um ciclo fechado, composto das seguintes etapas (figura 2):
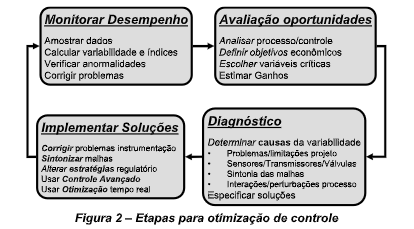
ANÁLISE DO PROCESSO, AVALIAÇÃO DE OPORTUNIDADES E BENEFÍCIOS: Conhecer o processo, operações unitárias, equipamentos, relações causa-efeito, interações, perturbações; verificação dos fluxogramas de processo e instrumentação (P&I), manuais e procedimentos de operação; definição dos objetivos econômicos da planta; escolher as variáveis críticas para o controle ligadas aos objetivos econômicos da planta; análise das estratégias de controle existentes; verificação da compatibilidade entre as estratégias e os objetivos de controle; estimativa dos benefícios possíveis. Um projeto de CA deverá ter objetivos econômicos claros, realistas e atingíveis. Os benefícios devem ser quantificados e verificados após sua implementação. A frustração por benefícios não alcançados pode inviabilizar futuros projetos. É importante conseguir o apoio e comprometimento de todos os envolvidos. Costumamos chamar esta etapa de “Avaliação de Oportunidades e Benefícios com Otimização do Controle”.
DIAGNÓSTICO DE VARIABILIDADE DO SISTEMA DE CONTROLE: Verificação do estado atual, problemas e limitações existentes em malhas de controle, controladores, elementos primários e elementos finais. Verificação de erros de projeto e operação fora das condições dos equipamentos. Coleta, tratamento de dados e cálculo estatístico das variabilidades. Determinação das causas da variabilidade. Atualmente os melhores sistemas digitais dispõem de ferramentas que facilitam enormemente estas tarefas. Após estas etapas dispomos de conhecimento suficiente para propor soluções que melhorem a variabilidade da planta de forma global, levando em consideração seus principais objetivos de controle. As soluções propostas devem seguir princípios que chamamos de “Inteligência Combinada”.
1. Procure por uma solução simples:
Uma solução simples é quase sempre a melhor solução. Uma solução complexa pode conseguir um resultado um pouco melhor, mas o custo pode ser muito elevado.
2. Use toda a informação disponível:
Ao resolver um problema, não desperdice informação disponível. Um tempo de atraso no processo pode facilmente ser visto na carta de tendência.
3. Não dependa da exatidão da informação:
Toda a informação obtida pode não ser exata. Por esta razão, a solução tem que ser bastante ágil ou adaptável para conviver com a inexatidão e incertezas.
4. Aplique uma técnica que se ajuste ao problema:
Uma vez que quase todos os métodos têm suas vantagens e desvantagens, por que discutir? Vamos usar a técnica que se ajusta à aplicação.
IMPLEMENTAÇÃO DAS SOLUÇÕES: Seguindo os princípios descritos acima, as soluções serão implementadas em ordem de complexidade crescente como, por exemplo, as descritas a seguir:
1. Corrigir os problemas existentes em válvulas, sensores e transmissores:
Sempre começaremos com uma etapa de correção dos problemas encontrados na instrumentação de campo. Para medidores e transmissores são válidas recomendações como: usar medidores de vazão “vortex”, magnético e “coriolis”; usar transmissores inteligentes para reduzir efeitos de temperatura e pressão; usar RTD e transmissores de temperatura com faixa estreita. Para a redução dos problemas de válvulas de controle como “stiction” e histerese, podemos usar posicionadores digitais inteligentes, válvulas com gaxetas e sedes de baixa fricção e haste de conexão direta; usar o tamanho e tipo de válvula adequada, adicionar caracterização de sinal para melhorar a sensitividade; usar variadores de velocidade quando possível.
2. Sintonizar corretamente as malhas de controle existentes:
A correta sintonia das malhas de controle exige conhecimento do objetivo de cada malha e sua interação com as outras. Algumas devem ter sintonia mais agressiva e outras mais relaxadas. Um bom exemplo é em geral a sintonia de nível que pode aproveitar a capacitância dos vasos para amortecer as variações nos pontos a jusante da planta. Os melhores sistemas digitais oferecem ferramentas destinadas a simplificar e automatizar o trabalho de sintonia. Apesar destas ferramentas a experiência continua sendo fundamental para o processo de sintonia, pois ele não segue uma “receita” sempre igual em todos os casos.
3. Modificar o projeto de forma a eliminar fontes de variabilidade quando possível:
Lembrando que é sempre melhor eliminar a variabilidade em sua origem que procurar atenuar usando a malha de controle, podemos adotar algumas medidas simples na fase de projeto da planta como: reduzir o tempo morto da válvula; reduzir o tempo de transporte no projeto de linhas e equipamentos; reduzir constante de tempo e tempo morto de medição; introduzir equipamentos que permitam a atenuação da variabilidade.
4. Alterar as estratégias de controle regulatório:
As estratégias de controle existentes devem ser revisadas quando estiverem erradas ou inadequadas aos objetivos de controle da planta. Verificamos frequentemente estratégias de controle equivocadas, resultado de erros de projeto ou simplesmente de cópias de erros em projetos semelhantes.
5. Utilizar tecnologias de Controle Avançado e Otimização:
O desempenho do controle oferecido pelo algoritmo PID muitas vezes não é suficiente para se obter a redução de variabilidade desejada. Este algoritmo tem sérias limitações para controlar processos com características difíceis como não-linearidade, interações com outros controladores, grande tempo-morto, dinâmicas e ganho variantes no tempo. Não tem características adaptativas e sua sintonia é sempre um problema. Nestes casos a solução é usar uma tecnologia de Controle Avançado. Estas tecnologias evoluíram nos últimos anos e tornaram-se opções viáveis para aplicações práticas. Ainda assim exigem alguns cuidados para sua correta utilização como:
- Devem ser projetadas de forma simples, suficientes para atingir o resultado desejado. Uma aplicação multivariável deve ter o menor tamanho possível para facilitar o entendimento de suas ações pelos Operadores;
- A tecnologia de CA deve ser conhecida e de resultados suficientemente comprovados em aplicações anteriores;
- Devem ter características como robustez, confiabilidade e disponibilidade. Sistemas sujeito à falhas e interrupções perdem a credibilidade dos Operadores que tendem a mantê-lo desligado. O sistema de controle deve facilitar o trabalho do Operador e jamais causar dificuldades adicionais;
- A ferramenta de CA usada deve ser integrada e padronizada. O uso do padrão OPC é recomendável. O tratamento das informações deve seguir o mesmo padrão do sistema digital. A interface gráfica de operação deve ser simples e manter as características da usada nos outros controladores. As mensagens geradas devem ser autoexplicativas e inteligentes;
- É fundamental a participação do Pessoal da planta no projeto. É indispensável a participação de Operadores. Com o sentimento de corresponsabilidade no projeto, eles serão os responsáveis por disseminar o conhecimento e zelar pelo bom desempenho do sistema;
- O treinamento deve proporcionar aos envolvidos com a operação da unidade um perfeito entendimento da tecnologia do controle. Deve ter aspectos teóricos com uso de simulação, e práticos do tipo “hands-on” assistido com supervisão;
- É de grande importância contar com a orientação de Consultores com experiência da implementação de projetos semelhantes. A experiência permite obter melhores resultados, facilita e reduz os prazos e custos na implementação.
MONITORAR O DESEMPENHO DO SISTEMA DE CONTROLE: Após sua implementação o sistema deve ser acompanhado de forma a manter sua boa operabilidade. Qualquer problema deve ser imediatamente corrigido. A estrutura e a sintonia das malhas devem ser mantidas atualizadas, de acordo com os objetivos e alterações da planta. Os componentes das malhas devem ter sua manutenção preventiva e corretiva priorizada. Sistemas desatualizados e com baixa disponibilidade são frequentemente desligados e abandonados pelos operadores. Esta costuma ser a maior causa de não realização dos lucros esperados com a implementação de Controle Avançado.